Wearable Robotics for Augmented Human Mobility & Functionality
Timeline
Oct 2024 - Jun 2025
TYPE
Academic
Engineering Design
Team Project
RoLE
Main Mechanical Designer
DELIVERABLEs
3D CAD model
Analysis
Physical Prototype
TOOLS
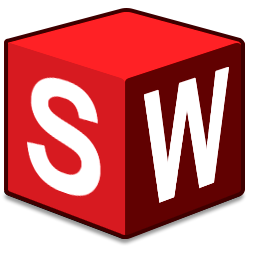
SolidWorks
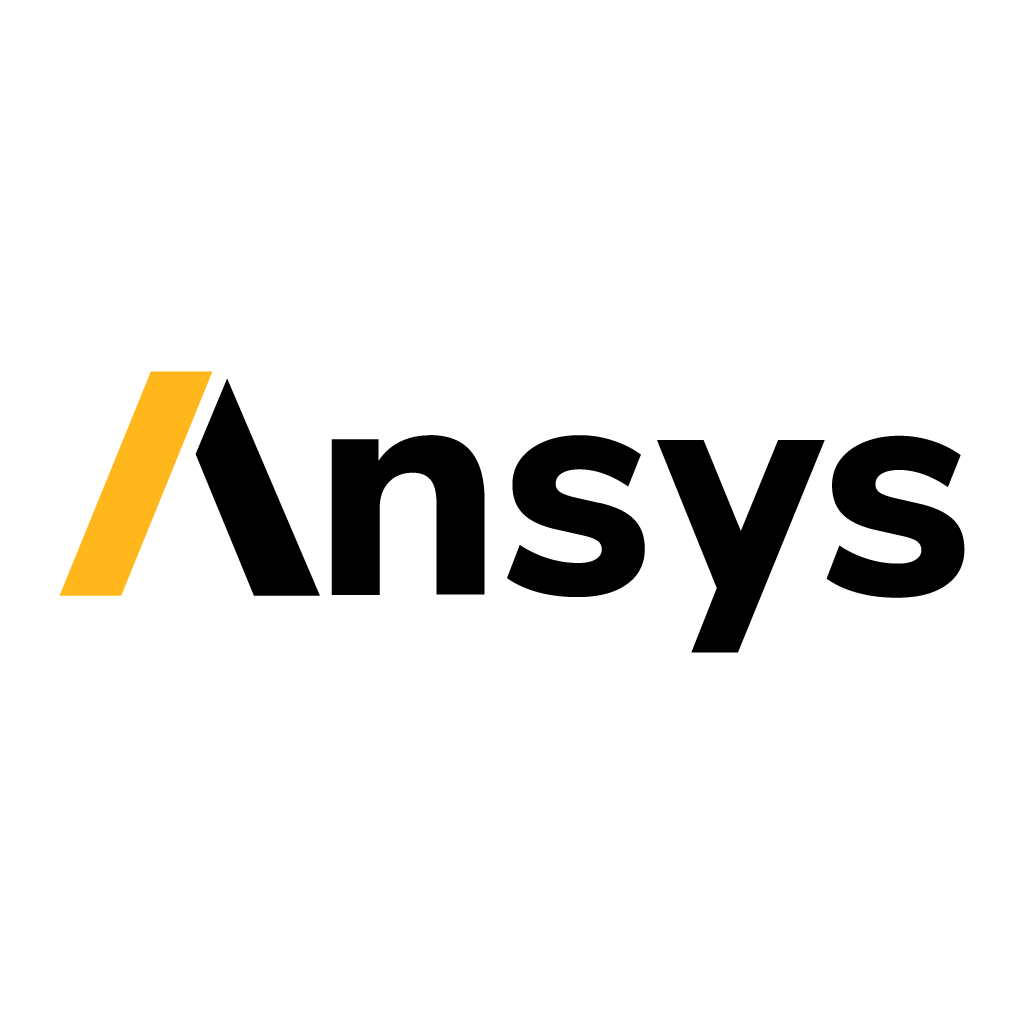
Ansys
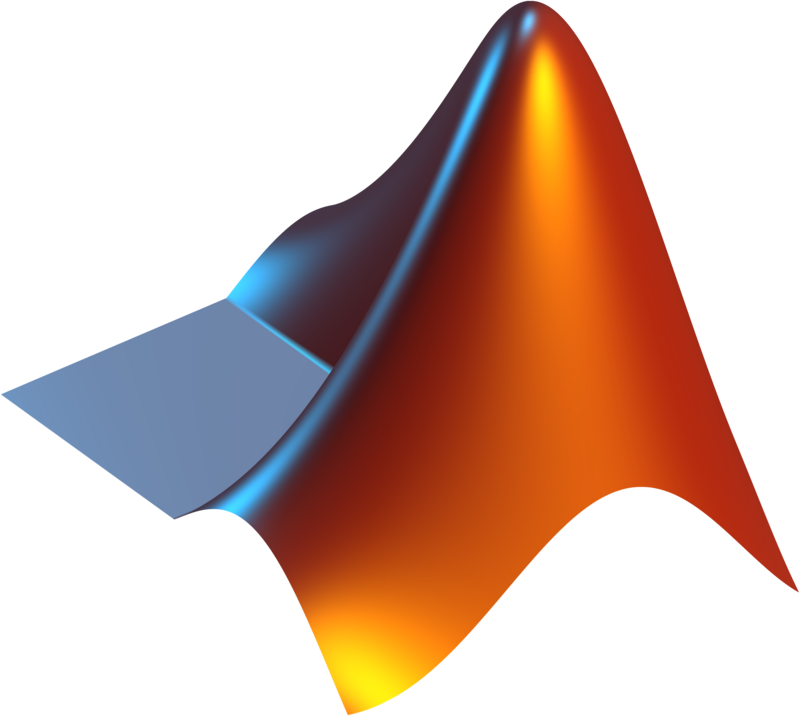
MATLAB
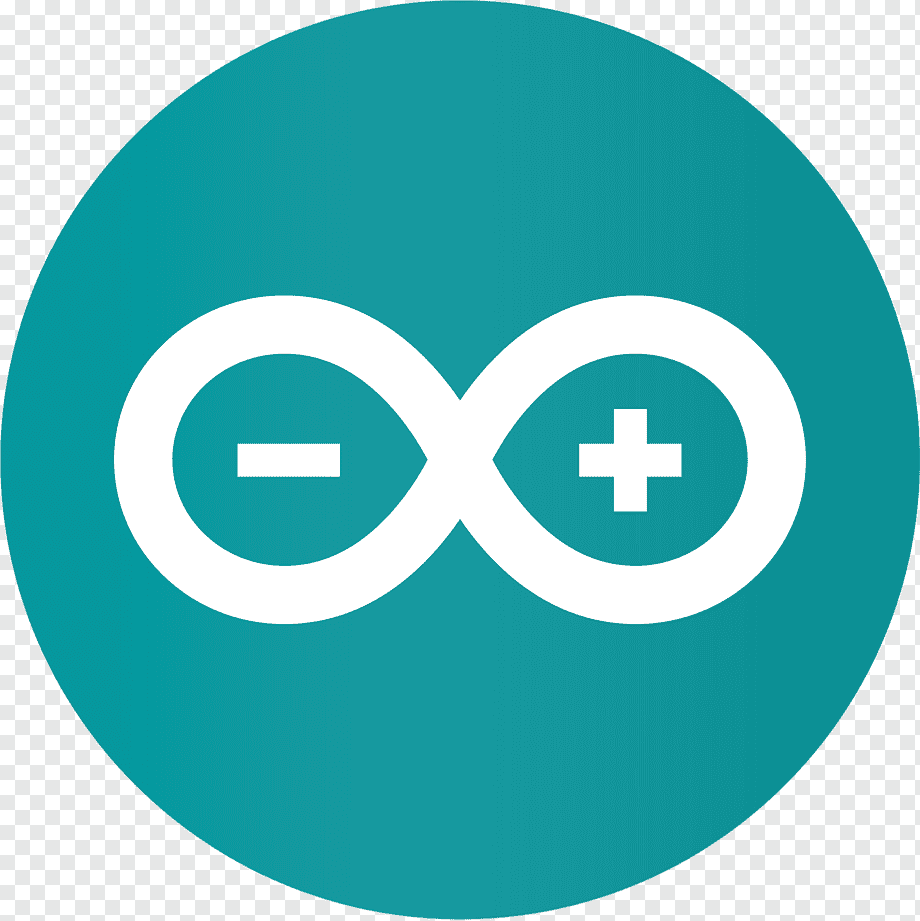
Arduino
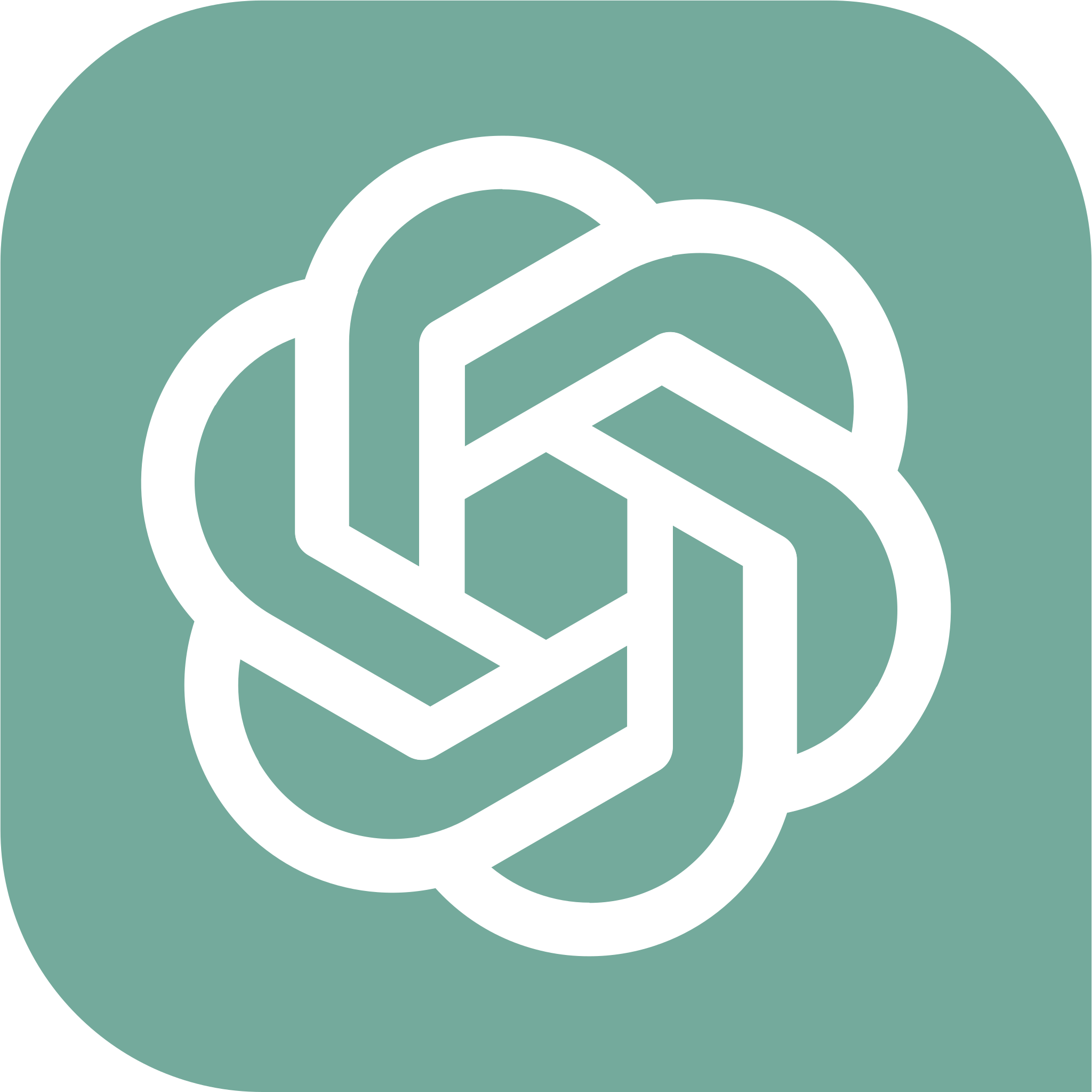
ChatGPT
This is an engineering design project that aims to create a device with Variable Stiffness Actuators (VSAs) to help patients in knee rehabilitation exercises. This is the capstone project for my Bachelor Degree at VinUniversity, and a collaboration of four students from different engineering background. I was the main mechanical designer of the team, I designed the device using SolidWorks, ran simulations using MATLAB and Ansys. I also collaborate in controlling the devices.
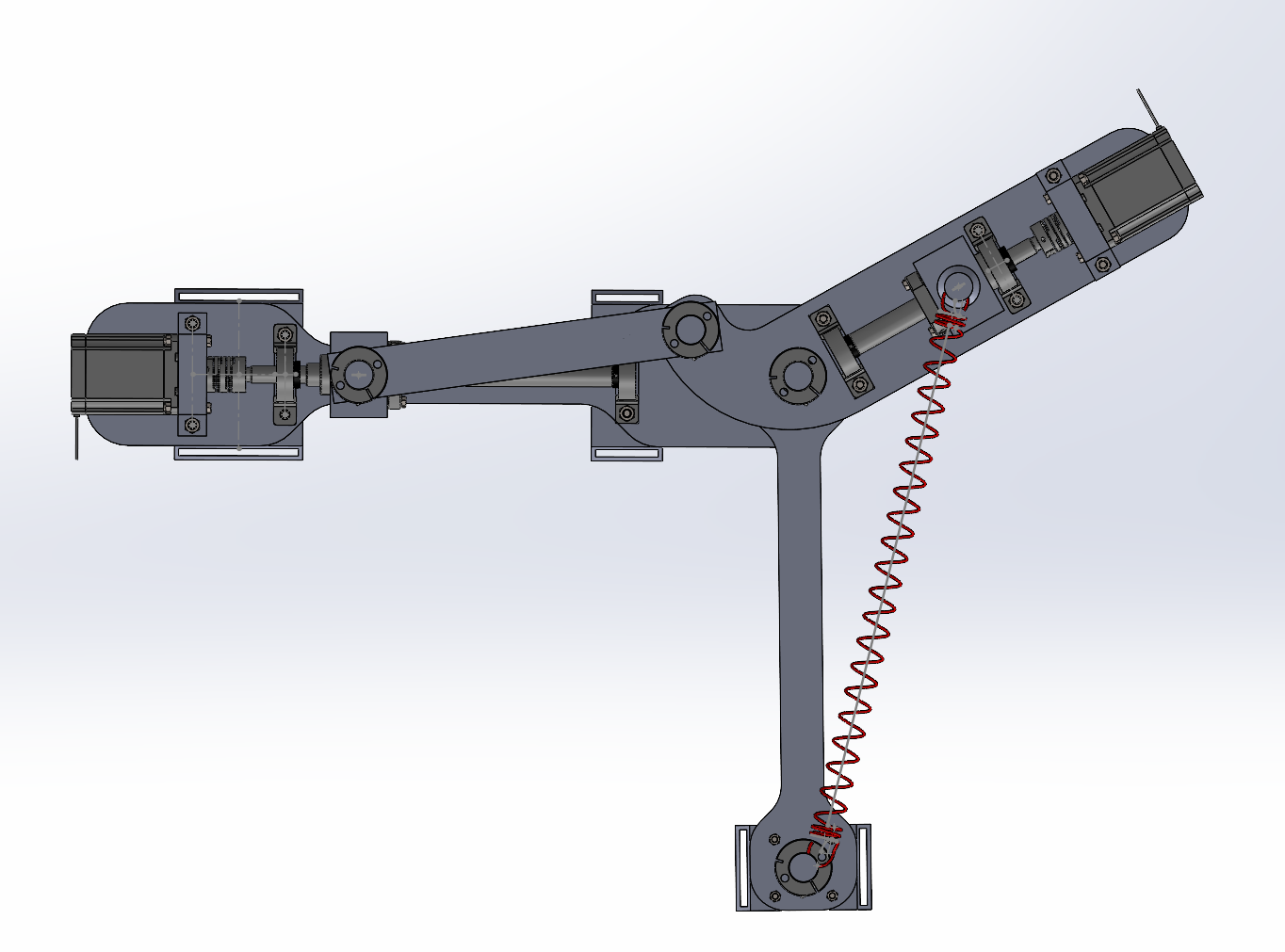
problem
Knee rehabilitation is an important part of the recovery process for patients after an accident or surgery. This is a slow and inefficient process and requires a lot of support from clinicians. This heavy reliance on clinical expertise not only limits scalability but also places significant strain on healthcare resources. This project explores the development of a variable stiffness actuator mechanism.
goal
Design a device to replicate the support from clinicians during knee rehabilitation exercises by using Variable Stiffness Actuators.
Members & Responsibilities
Supervisor Professor
Provide assistance and guidance for the team. Help members navigate through obstacles to receive the desired result.
Duy-Quang (it's Me)
Responsible for Mechanical Design & Analysis. Design the core mechanisms and elements of the device.
Collab in System Control.
Collab in System Control.
Member 2
Responsible for Manufacturing. In charge of material selections, manufacturing methods and executions.
Collab in System Control.
Collab in System Control.
Member 3
Responsible for Electrical Design. Responsible for the electrical components, focus on EMG signal processing & data gathering.
Collab in System Control.
Collab in System Control.
Member 4
Responsible for AI application. Focus on training AI model to predict angle output from inputs of EMG signals.
Collab in System Control.
Collab in System Control.
THE Design PROCESS
I. Literature Review:
Approaching this project, first our team decided to examine the previous approach related to VSAs through scientific entries and current products on the market. With the help of our supervisor professor, our team decided on the mechanism that we would use in our device.
Characteristics of variable stiffness actuator
Adjustable stiffness
Can change its stiffness (or compliance) in response to different conditions. Useful for situations where adaptability is crucial.
Elastic Components
VSAs usually utilize an elastic component in the actuators, often a spring.
Two motors
Usually the devices use two motors to dynamically control the stiffness of the system.
Control & Sensing
The device need sensors to understand the real-time situation to adjust the stiffness accordingly.
II. IdeatION:
After investigating the basics of VSAs, our team map out the core elements of this projects. We decide to take a very simple approach.
Elements of our device
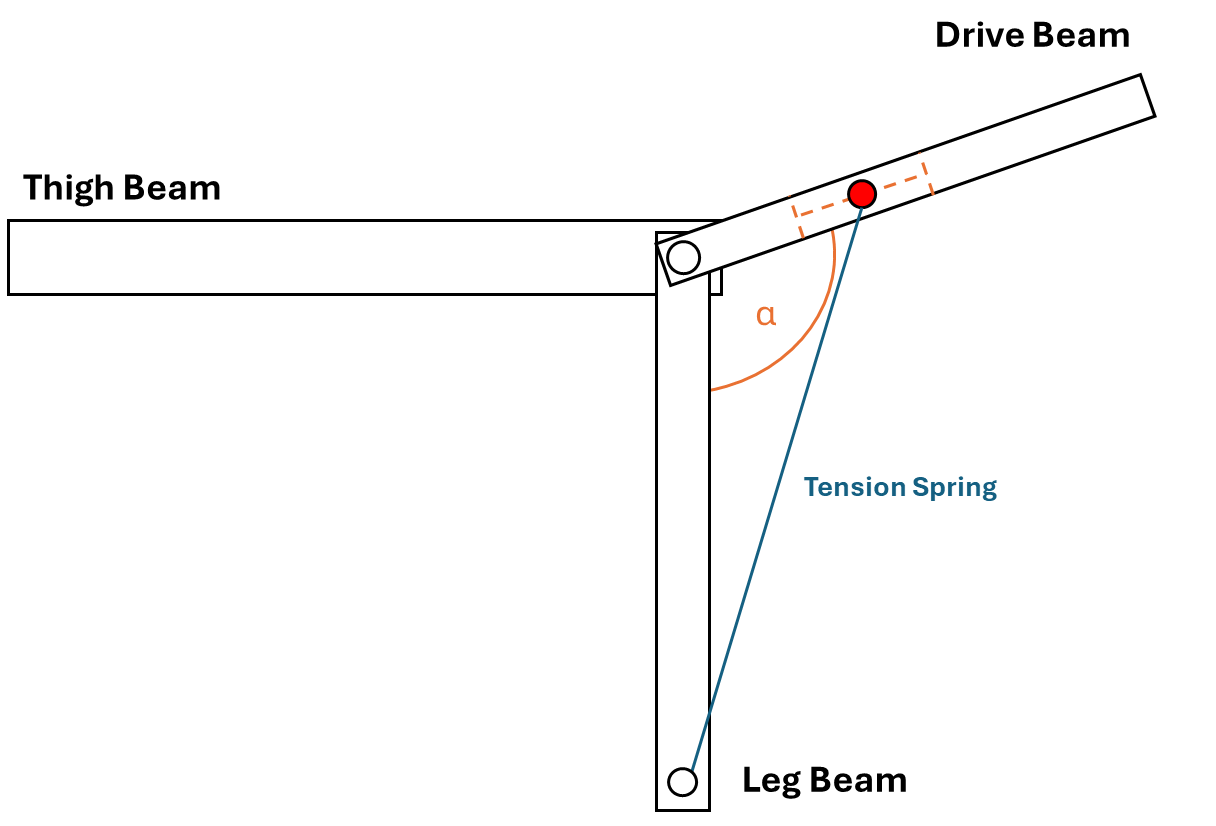
Frame
Consists of 3 main beams. One beam is attached to the user's thigh, another to the leg at the ankle level. The third beam is the drive beam.
Elastic Components
Tension springs would be the most suitable for this project. The spring will be attached between the drive beam and the leg beam.
Motors
Two high-torque stepper motors. One motor control the angle of the drive beam, the other control the distance of the spring pin to the center axis.
Principle
One motor control the angle of the drive beam. One motor control the position of the spring pin. Spring stiffness is dynamically adjusted.
Sensing
Use EMG sensors to get the electrical signals when the user move their legs. This signal is then used to control the motor accordingly.
Machine learning
Apply Machine Learning in the controlling process. AI model receive EMG signal as inputs and give out preference angle.
As the main Mechanical Designer, my responsibilities revolve around design the frames & mechanisms, choosing springs and motors. I also participate in the controlling process, providing mechanical insights.
I decided to use SolidWorks to visualize our idea, also to investigate the potential mechanisms to control the drive beam.
Early Stage - Low Fidelity Design - SolidWorks
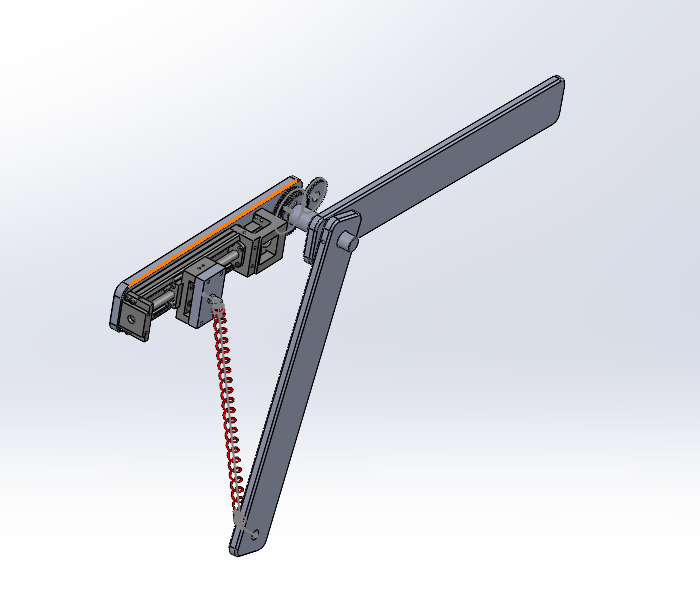
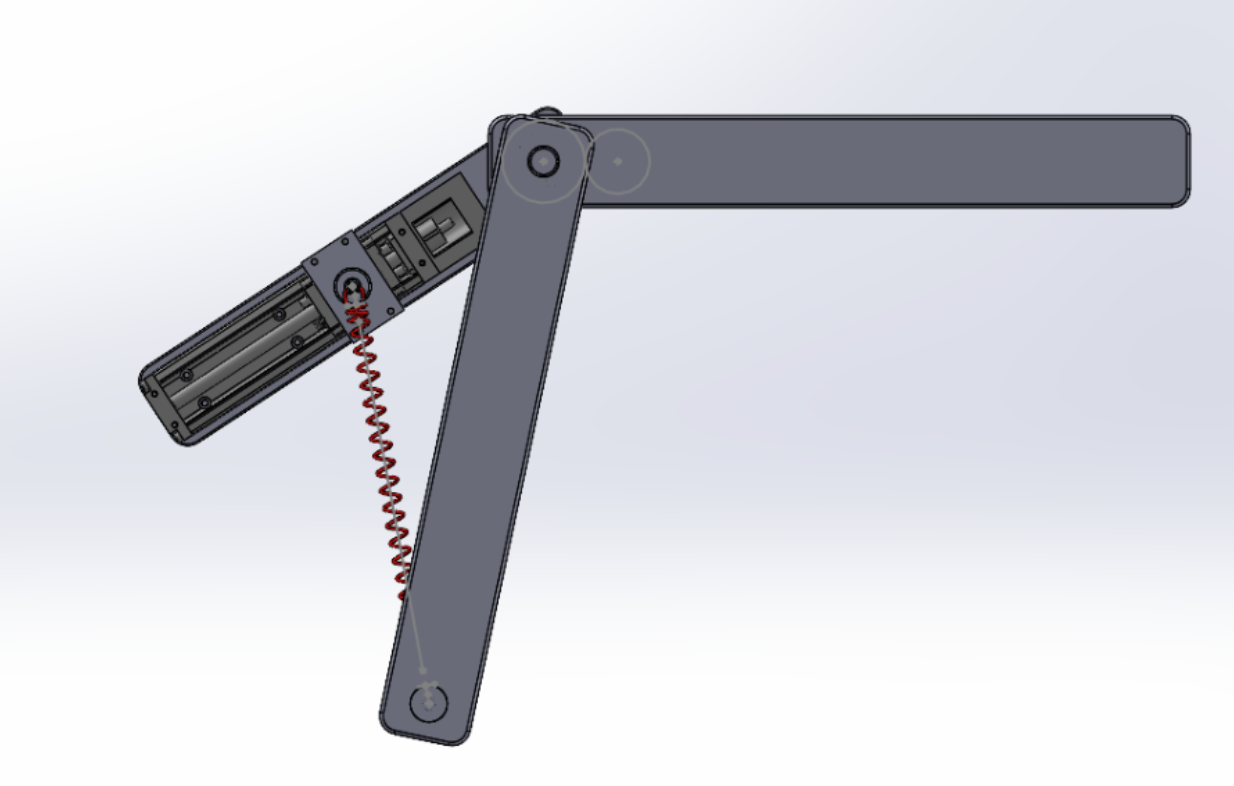
III. Mechanical Design:
After experimenting with different approach in SolidWorks, along with the guidance of our professor, our team decided that we would use two set of ball screw that convert the rotational motions of the motors to linear motions. The linear motions will then be used to control the angle of the drive beam through the principle of the crank-slider mechanism.
Mechanism Design
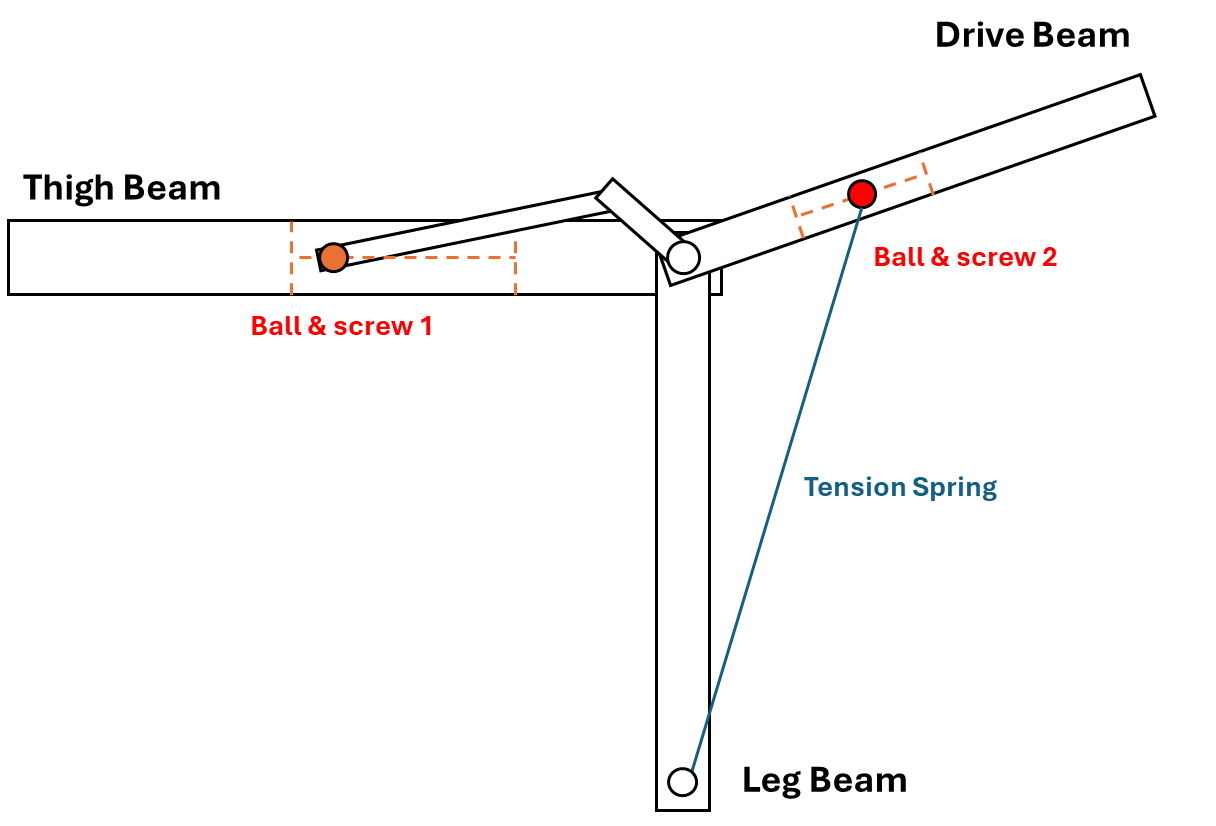
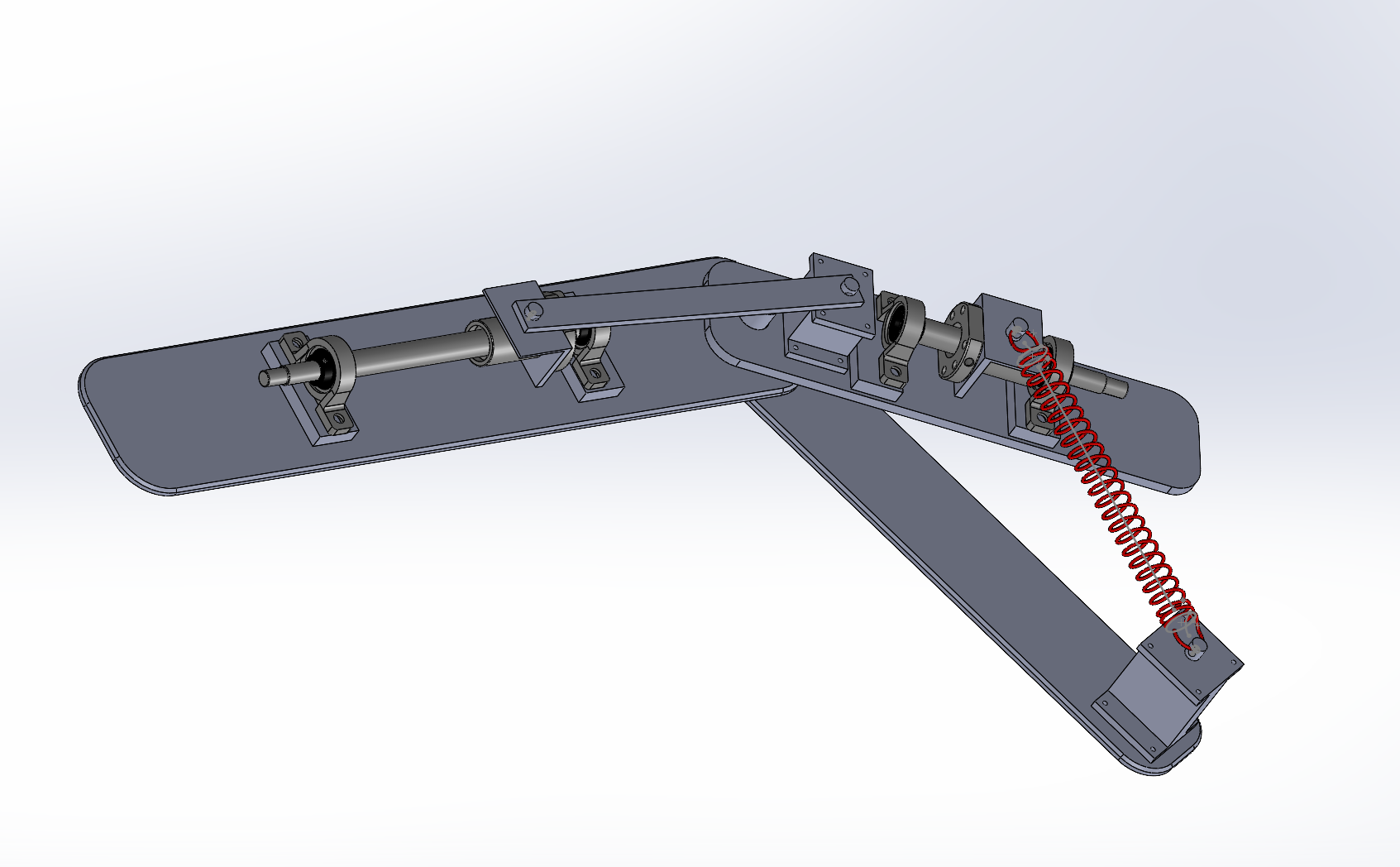
After deciding on the mechanism, I started working on the high-fiedlity design.
High Fidelity Design - SolidWorks
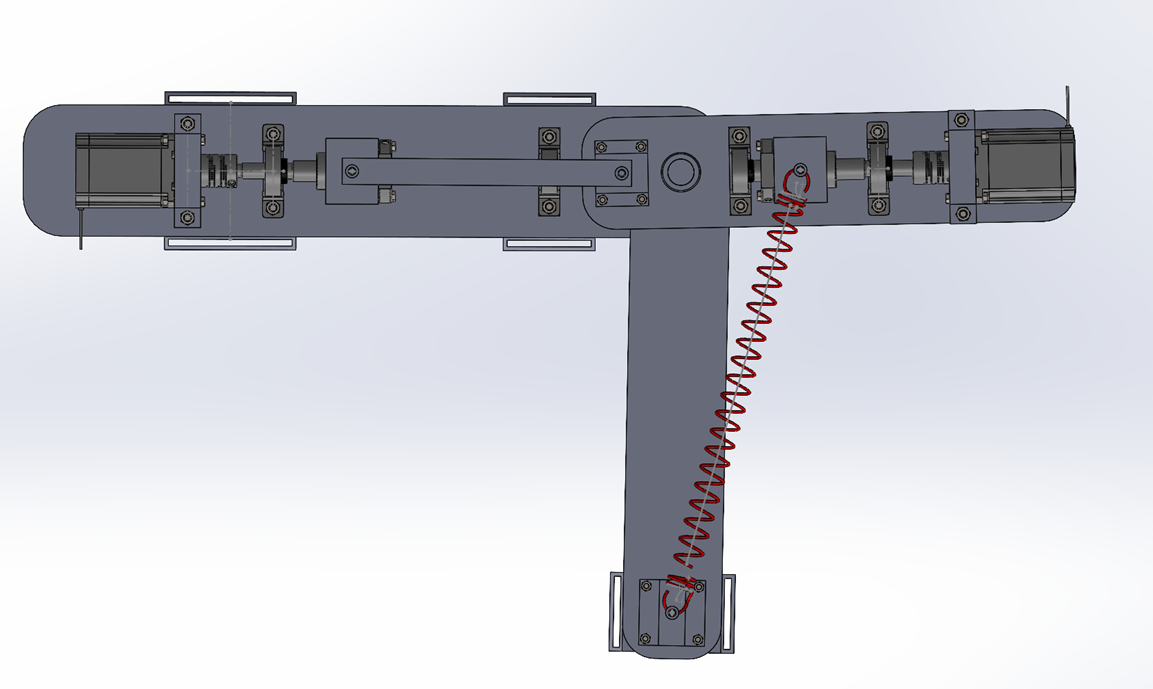
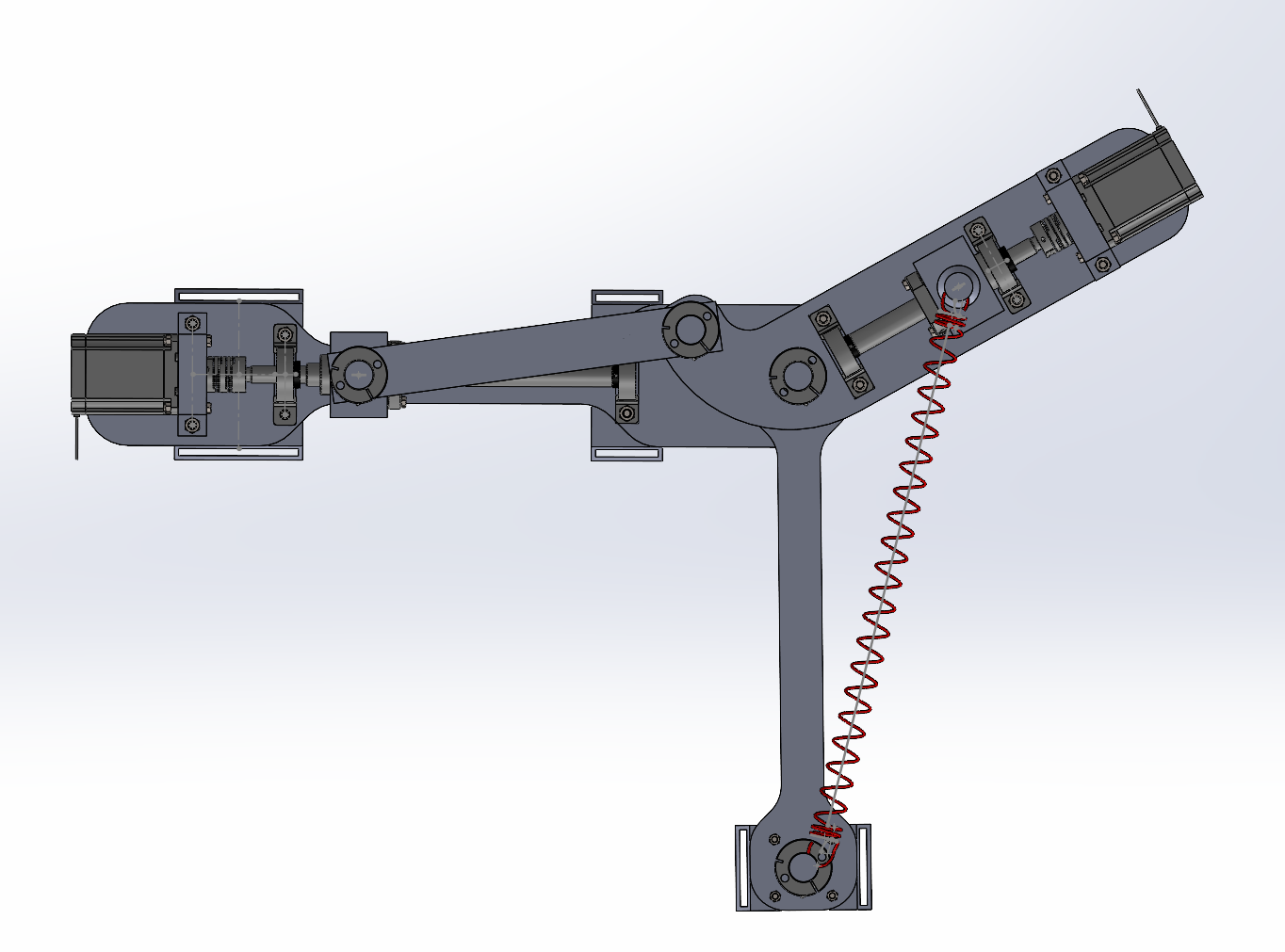
IV. Prototyping:
With the High Fidelity Design, I exported the necessary files and give clarifications for another member to manufacture the necessary part for the physical prototype. The beams will be made by laser cutting MICA plates. The axes will be made by CNC-ing steel pieces. Other elements will be bought or 3D printed.
I also use MATLAB with the help of ChatGPT to create a simulation of the device.
MATLAB Simulation
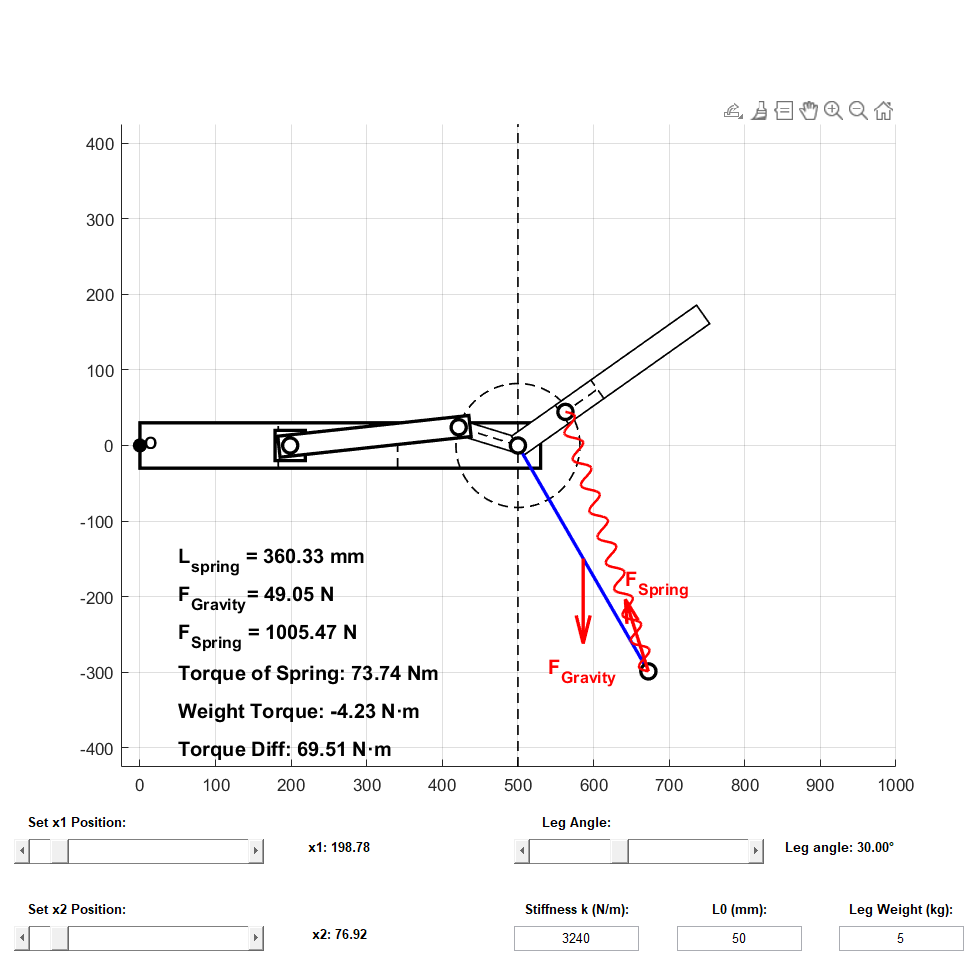
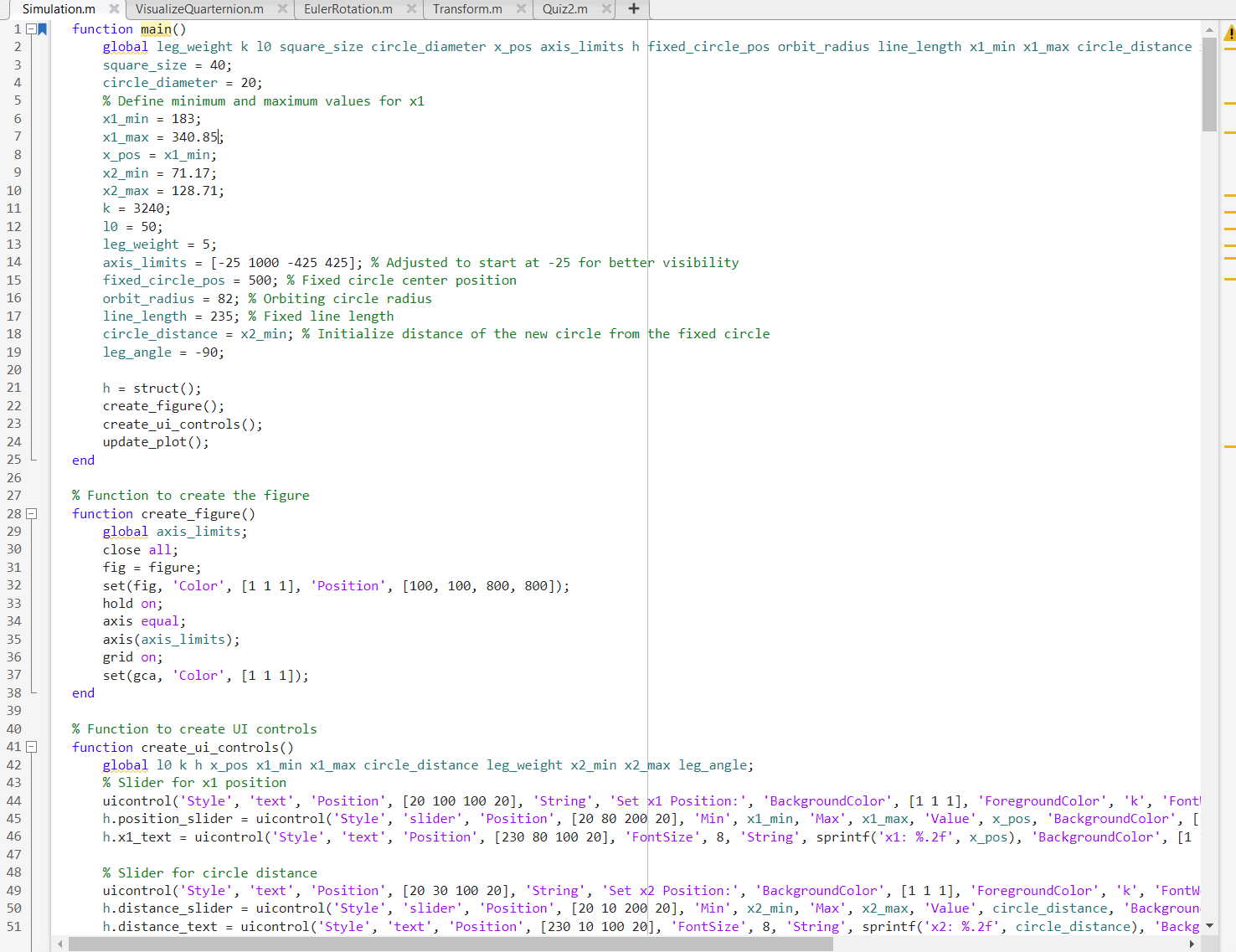
This simulation provide me with a brief understanding of the torque relationships, helping me in choosing the right tension spring and motor for the project.
Currently, I am in the process of examining the strength of the beams using ANSYS.
V. Refine The Design:
After manufacturing the beams, our team realize that the placement of the Velcro straps makes it impossible to strap the beams to the leg. Currently, I am finding alternatives to fix this issue.
This Project is still in Progress.